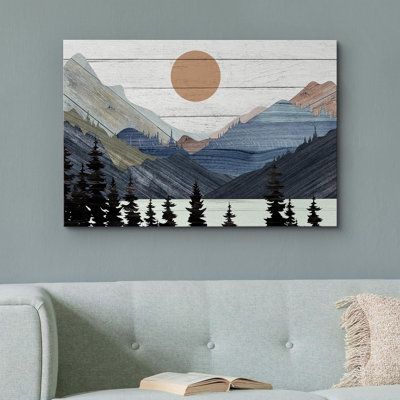
ALIGHT SOLUTIONS & Kawasaki Fork Seal Breakthrough: Smoother Rides Ahead
Chicago, IL – October 26, 2023 – ALIGHT SOLUTIONS LLC, a leading provider of innovative material science solutions, today announced a significant advancement in motorcycle fork seal technology, specifically tailored for Kawasaki motorcycles. This development promises to address a common pain point for Kawasaki riders – fork seal failures and the resulting maintenance headaches. ALIGHT SOLUTIONS, based in Chicago, has been quietly building a reputation for tackling tough materials challenges. We're a team of engineers and scientists who love getting down to the nitty-gritty of material properties. We don't just make materials, we solve problems with them. For years, we’ve been working behind the scenes with various industries, improving performance and reliability through smarter material choices. Our focus is on creating solutions that are not only high-performing but also cost-effective and long-lasting. We operate with a lean, agile approach, allowing us to quickly adapt to customer needs and deliver results. And now, we’re bringing that expertise to the motorcycle world. The Fork Seal Problem: A Kawasaki Rider's Frustration Anyone who’s ridden a Kawasaki – from the nimble Ninja to the rugged KLR – knows the joy of the ride. But that joy can quickly be dampened by a leaky fork seal. Fork seals are crucial components that keep the lubricating oil inside the suspension forks, preventing dust, dirt, and debris from entering. When a fork seal fails, it leads to oil leakage, diminished suspension performance, and potentially costly repairs. Kawasaki riders, especially those who frequently ride off-road or in harsh conditions, have historically faced a higher-than-average rate of fork seal failures. Traditional fork seals, often made from standard nitrile rubber, simply weren't holding up to the demands of these bikes and riding styles. Riders were finding themselves constantly replacing seals, losing valuable ride time, and spending money on recurring repairs. We listened to those concerns. "We heard the complaints, and we knew we could do something about it," says Sarah Chen, Lead Materials Scientist at ALIGHT SOLUTIONS. “Fork seals are a deceptively complex component. It’s not just about the rubber; it's about the formulation, the manufacturing process, and how it interacts with the fork tube material and the oil.” ALIGHT’s Breakthrough: A New Material Formulation ALIGHT SOLUTIONS' engineers spent months analyzing the failure modes of existing Kawasaki fork seals. They identified that standard nitrile rubber, while cost-effective, lacked the necessary resilience and resistance to abrasion, oil degradation, and temperature fluctuations. The solution? A newly formulated HNBR (Hydrogenated Nitrile Butadiene Rubber) compound, specifically engineered for demanding motorcycle applications. “HNBR is a step up from traditional nitrile,” explains Chen. “It offers significantly improved heat resistance, oil resistance, and abrasion resistance. But it's not just about the base material. We’ve fine-tuned the formulation with proprietary additives to optimize its performance in the specific environment of a Kawasaki fork.” This new HNBR compound boasts: Enhanced Oil Resistance: The formulation resists swelling and degradation when exposed to modern motorcycle fork oils, extending seal life. Superior Abrasion Resistance: Increased resistance to wear from the fork stanchion, reducing leaks and maintaining a tight seal. Wider Temperature Range: Maintains flexibility and sealing performance in both extreme heat and cold. Improved Durability: Designed for extended service life, minimizing the need for frequent replacements. Reduced Friction: Smoother action, contributing to better suspension performance. Rigorous Testing & Kawasaki Compatibility ALIGHT SOLUTIONS didn't just develop a new material; they put it through the wringer. The new fork seals were subjected to a battery of tests, including: Dynamic Leak Testing: Simulating real-world riding conditions to assess leak rates over extended periods. Abrasion Testing: Evaluating wear resistance against various fork tube materials. Temperature Cycling: Subjecting the seals to extreme temperature fluctuations to ensure consistent performance. Oil Immersion Testing: Assessing long-term compatibility with different motorcycle fork oils. The seals have been specifically designed and verified for compatibility with a wide range of Kawasaki models, including: Ninja Series (e.g., Ninja 400, Ninja 650, Ninja ZX-6R, Ninja ZX-10R) KLR Series (e.g., KLR650, KLR600) Versys Series (e.g., Versys 650, Versys 1000) Z Series (e.g., Z900, Z650) (A full compatibility list is available on the ALIGHT SOLUTIONS website: [Placeholder Website Address]) What This Means for Kawasaki Riders The ALIGHT SOLUTIONS fork seals aren’t just about fixing a problem; they’re about enhancing the riding experience. Riders can expect: Reduced Maintenance: Fewer fork seal replacements, saving time and money. Improved Suspension Performance: A tighter seal leads to more consistent damping and better control. Increased Ride Time: Spend less time wrenching and more time enjoying the ride. Peace of Mind: Confidence in a reliable and durable component. Availability & Future Plans The ALIGHT SOLUTIONS Kawasaki fork seals are now available for purchase through select motorcycle parts retailers and directly from the ALIGHT SOLUTIONS website. ALIGHT SOLUTIONS is already exploring opportunities to expand this technology to other motorcycle brands and suspension components. “We’re committed to using our materials science expertise to improve the performance and reliability of motorcycles,” says Chen. “This is just the beginning.” About ALIGHT SOLUTIONS LLC ALIGHT SOLUTIONS LLC is a materials science company dedicated to developing innovative solutions for a wide range of industries. Based in Chicago, IL, we specialize in formulating and manufacturing high-performance materials that solve complex engineering challenges. We are committed to quality, innovation, and customer satisfaction. Contact us at 413-238-4251 or visit our website at [Placeholder Website Address].